Fasteners and Machining: Key to Efficient and Reliable Manufacturing
Navigating the World of Fasteners and Machining: Strategies for Accuracy and Rate
In the intricate realm of fasteners and machining, the quest for accuracy and rate is a continuous challenge that demands careful interest to information and critical planning. From comprehending the varied variety of bolt types to picking optimum products that can hold up against rigorous needs, each step in the process plays an essential duty in attaining the wanted result.
Understanding Bolt Kind
When selecting fasteners for a job, recognizing the various types offered is important for ensuring optimal performance and integrity. Screws are used with nuts to hold products with each other, while screws are flexible fasteners that can be utilized with or without a nut, depending on the application. Washing machines are necessary for distributing the lots of the fastener and preventing damages to the product being secured.
Picking the Right Materials
Recognizing the significance of selecting the appropriate products is extremely important in making certain the optimum efficiency and reliability of the selected bolt types discussed formerly. When it comes to fasteners and machining applications, the product option plays a critical duty in figuring out the general strength, resilience, deterioration resistance, and compatibility with the desired setting. Various products use varying residential or commercial properties that can dramatically affect the performance of the fasteners.
Typical materials utilized for bolts consist of steel, stainless steel, brass, aluminum, and titanium, each having its unique staminas and weak points. Steel is renowned for its high stamina and durability, making it suitable for a broad array of applications. Selecting the right product includes considering elements such as stamina demands, environmental problems, and budget plan constraints to guarantee the wanted performance and longevity of the fasteners.
Accuracy Machining Techniques
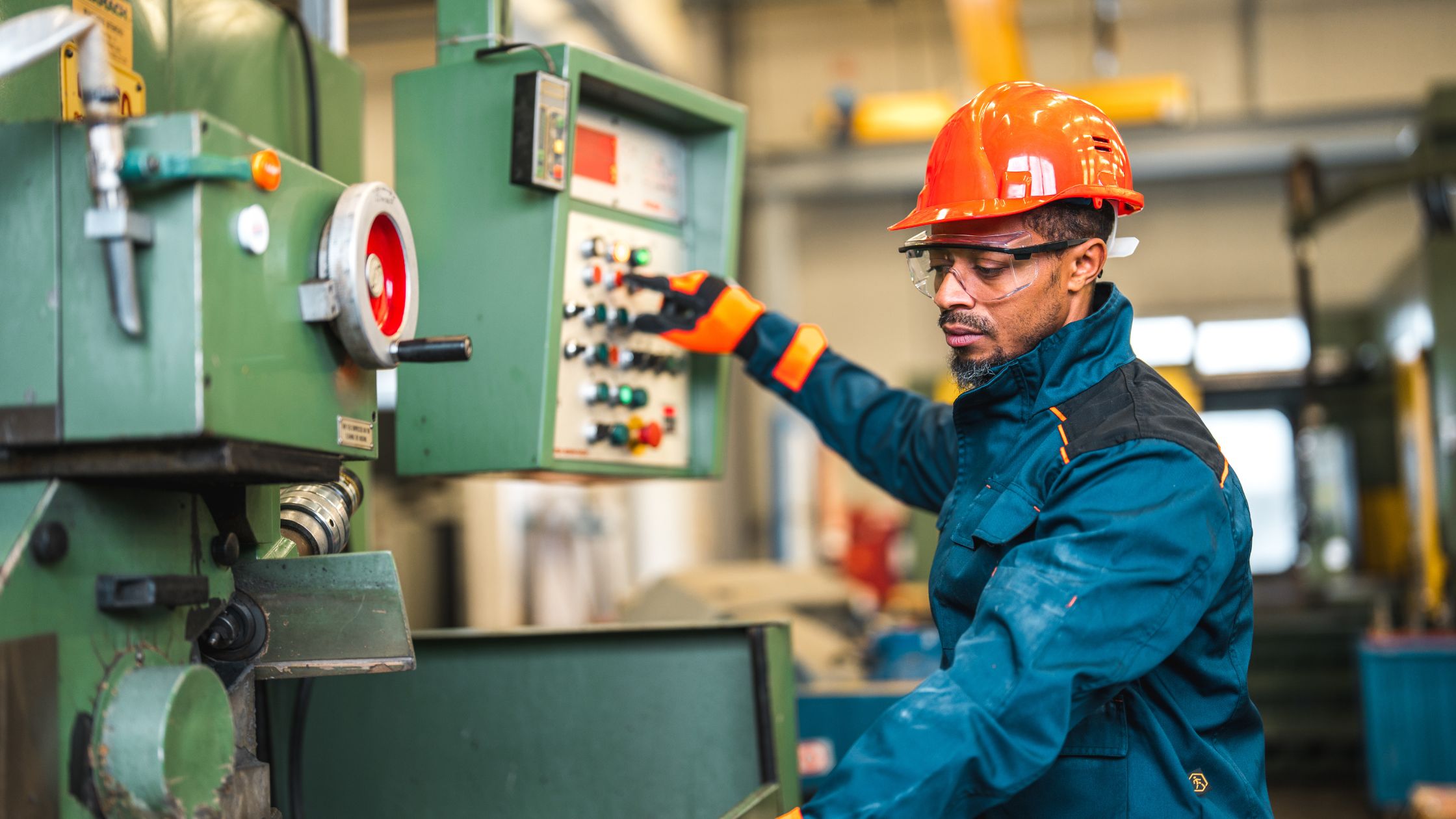
Along with CNC machining, other accuracy techniques like grinding, turning, milling, and drilling play essential functions in fastener manufacturing. Grinding helps accomplish great surface coatings and tight dimensional tolerances, while transforming is often utilized to develop cylindrical parts with exact diameters. Milling and drilling procedures are vital for forming and creating holes in bolts, guaranteeing they meet specific specs and function properly.
Enhancing Rate and Performance
To optimize bolt manufacturing processes, it is important to streamline procedures and carry out effective strategies read this post here that complement precision machining techniques. One vital technique for improving rate and effectiveness is the application of lean production principles. By decreasing waste and concentrating on continuous enhancement, lean practices aid enhance and get rid of traffic jams process. In addition, investing in automation modern technologies can dramatically improve manufacturing speed. Automated systems can manage repeated tasks with precision and speed, permitting workers to concentrate on even more complex and value-added tasks. Taking On Just-In-Time (JIT) stock management can also improve performance by guaranteeing that the appropriate materials are readily available at the appropriate time, decreasing excess inventory and reducing lead times. Promoting a society of cooperation and interaction among group participants can improve general performance by advertising transparency, problem-solving, and technology. By incorporating these strategies, producers can accomplish a balance in between rate and precision, eventually enhancing their one-upmanship in the bolt sector.
Top Quality Control Steps
Executing rigorous top quality control actions is vital in making sure the reliability and consistency of bolt products in the manufacturing procedure. Fasteners and Machining. Quality control steps include different stages, beginning from the option of raw products to the last examination of the finished bolts. This includes evaluating aspects such as product strength, make-up, and durability to assure that the fasteners fulfill industry standards.
Routine calibration of tools and machinery is imperative to keep consistency in manufacturing and make certain that fasteners satisfy the necessary tolerances. Implementing stringent protocols for recognizing and addressing flaws or non-conformities is essential in stopping substandard products from going into the marketplace. By developing a thorough top quality control structure, producers can maintain the track record of their brand name and deliver fasteners that meet the highest my response possible criteria of performance and sturdiness.
Final Thought
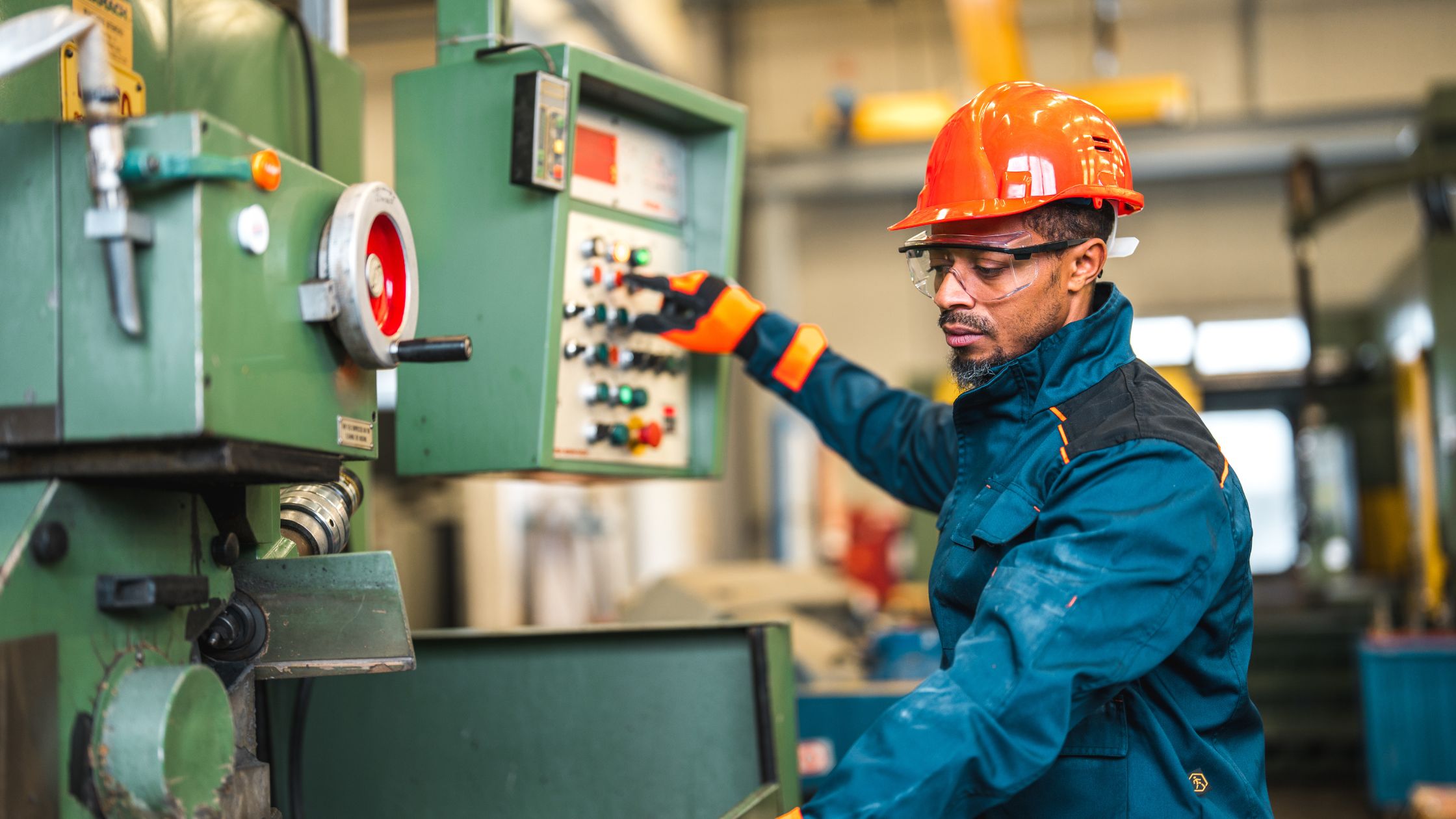
In the complex realm of bolts and machining, the pursuit for precision and rate is a perpetual challenge that requires precise focus to information and calculated planning. When it comes to fasteners and machining applications, the product option plays a critical duty in figuring out the general toughness, resilience, corrosion see resistance, and compatibility with the designated atmosphere. Accuracy machining involves different advanced approaches that guarantee the tight tolerances and requirements needed for fasteners.In enhancement to CNC machining, various other precision methods like grinding, turning, milling, and boring play crucial functions in bolt manufacturing.To maximize fastener production procedures, it is important to enhance operations and apply efficient approaches that match precision machining techniques.